What is PTFE Membrane?
First developed in early 1940s by a subsidiary of DuPont® chemicals, PTFE quickly proved its usefulness in many applications such as a coating for valves and pipes used to carry highly reactive uranium hexafluoride used during uranium production for the Manhattan Project during the Second World War. Besides its most famous application as a non-stick coating for cookware, PTFE is used in many industrial and commercial applications where low fiction and high durability are needed such as bearings, gears, etc.
PTFE membrane is a layer of PTFE material that removes particles of a certain size and shape, while allowing others to pass through. When applied to a substrate (such as fiberglass, P90, etc.) it removes particles much like dustcake normally would on a Baghouse filter. * See section “The Benefits of Surface Filtration”
Higher Efficiencies Using PTFE Filters
With its unique physical properties, Baghouse filters with PTFE membrane are able to out perform nearly all other filter constructions in many applications. Among its many useful properties, PTFE is hydrophobic (Literally “afraid of water”) meaning it repels water. Additionally, it has a very low coefficient of friction of 0.05 – 0.10 (meaning substances have a hard time sticking to it and are easily removed) and has a high melting point of approximately 325°C.
Stricter governmental regulations for particulate emission are on the horizon. The new EPA PM2.5 standard for particulate matter emissions will present additional challenges for facilities to reach compliance. Be ready to meet the challenge by employing high efficiency PTFE filter bags in your Baghouse.
PTFE filter bags from Baghouse.com can reach amazing efficiencies when operated deployed correctly. PTFE filters from Baghouse.com can easily reach sub-micron filtration ranges. In some applications efficiencies are high enough to allow for the recirculation of treated air back into the facility. Use of such “Green Technology” further promotes an environmentally friendly operation, and saves on heating costs.
Efficiency Claims Confirmed By EPA Testing
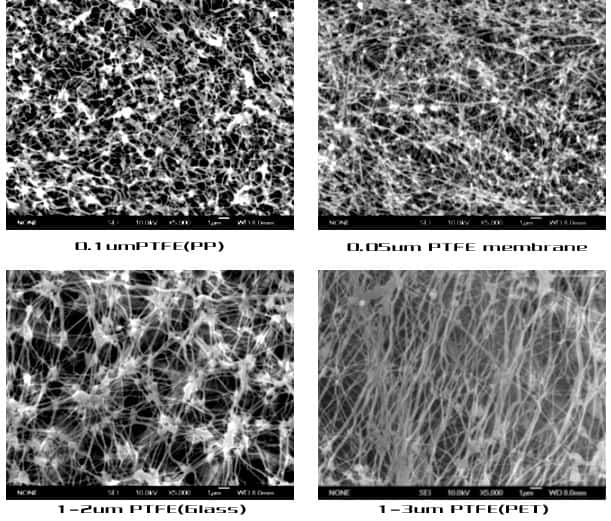
Independent testing conducted under the EPA’s Environmental Technology Verification (ETV) program has proven that PTFE Membrane filters are capable of ultra high efficiencies. Tests of PTFE filter bags from several different manufacturers showed particulate matter outlet emissions as low as 0.0006 gr/ACF (1.3mg/m3).
In most size ranges the test PTFE fabrics showed zero emissions during testing. Emissions data were below the detection limits of the testing equipment. The fractional efficiency percentages were 100%, only dipping to 99.98% with particle sized 0.3-0.5 (μM).*
Higher Efficiencies Using PTFE Filters
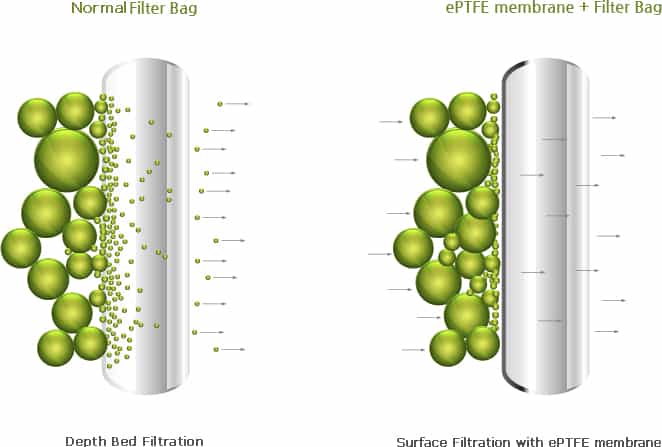
With its unique physical properties, Baghouse filters with PTFE membrane are able to out perform nearly all other filter constructions in many applications. Among its many useful properties, PTFE is hydrophobic (Literally “afraid of water”) meaning it repels water. Additionally, it has a very low coefficient of friction of 0.05 – 0.10 (meaning substances have a hard time sticking to it and are easily removed) and has a high melting point of approximately 325°C.
Stricter governmental regulations for particulate emission are on the horizon. The new EPA PM2.5 standard for particulate matter emissions will present additional challenges for facilities to reach compliance. Be ready to meet the challenge by employing high efficiency PTFE filter bags in your Baghouse.
PTFE filter bags from Baghouse.com can reach amazing efficiencies when operated deployed correctly. PTFE filters from Baghouse.com can easily reach sub-micron filtration ranges. In some applications efficiencies are high enough to allow for the recirculation of treated air back into the facility. Use of such “Green Technology” further promotes an environmentally friendly operation, and saves on heating costs.
The Benefits of Surface Filtration Over Depth Filtration
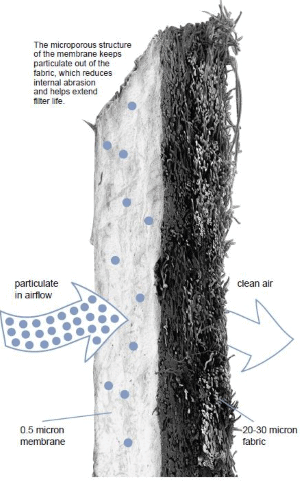
PTFE membrane filters also have a distinct advantage over non-membrane filters due to differences in the way they filter out particulate. Non-PTFE membrane filter bags employ depth filtration to filter particulate. Depth filtration is accomplished when a layer of dustcake forms on the outside of the filter, and an accumulation of dust particles is deposited in the depth of the filter. In coming particles are captured as they follow the tortuous path through the dustcake, and depth of the filter. As time goes on, more and more particles get trapped within the filter, leading to higher pressure drops and eventually filter “blinding” which reduces filter life.
Baghouse filters with a PTFE membrane however employ surface filtration to remove incoming particles. The PTFE membrane works as the primary filter cake, collecting all of the particulate on the surface. This keeps the particulate from penetrating the filter fabric, which can lead to reduced airflow, and filter “blinding”.
Additionally, with traditional filters larger than normal emission occur during start-up and immediately following the cleaning cycle due to lack of primary dustcake. With PTFE filters, this problem is largely eliminated.
PTFE Fabric Combinations
PTFE membrane can be applied to a large variety of fabric substrates depending on the particular application. Contact a Baghouse.com representative to help you to determine which combination of fabric and PTFE membrane is the best fit your particular process environment. Below is listing of several popular PTFE / Fabric combinations:
FABRICS | POLYPROPYLENE | ACRYLIC | POLYESTER | PPS | ARAMID | P84*** | FIBERGLASS* | PTFE FELT |
---|---|---|---|---|---|---|---|---|
Max Continuous Operating Temperature | 170°F (77°C) | 265°F (130°C) | 275°F (135°C) | 375°F (190°C) | 400°F (204°C) | 356–500°F (180–260°C) | 500°F (260°C) | 500°F (260°C) |
Abrasion | Excellent | Good | Excellent | Good | Excellent | Fair | Fair | Good |
Energy Absorption | Good | Good | Excellent | Good | Good | Good* | Fair* | Good |
Filtration Properties | Good | Good | Excellent | Excellent | Excellent | Excellent | Fair | Fair |
Moist Heat | Excellent | Excellent | Poor | Good | Good | Good | Excellent | Excellent |
Alkalines | Excellent | Fair | Fair | Excellent | Good | Fair | Fair | Excellent |
Mineral Acids | Excellent | Good | Fair | Excellent | Fair | Good | Poor** | Excellent |
Oxygen (15%+) | Excellent | Excellent | Excellent | Poor | Excellent | Excellent | Excellent | Excellent |
*SENSITIVE BAG-TO-CAGE | **FAIR WITH CHEMICAL- OR ACID-RESISTANT FINISHES | ***MUST OVERSIZE BAG FOR SHRINKAGE ABOVE 450°F (232°C) |
Differential Pressure (Pressure Drop) Advantages of PTFE Filters
How does the use of PTFE membrane Baghouse Filters Result in Lower System Pressure Drop?
Pressure drop in a Baghouse occurs for two factors that make it more difficult for air to pass through the filter:
1. The dustcake characteristics (thickness, density, composition, etc.)
2. The amount of particulate matter that is embedded within the fabric.
Initial pressure drop on fabric filters in general is not a reliable guide for how the filter will operate under load conditions. The addition of PTFE membrane to standard filter fabrics will on average lower initial permeability from 30-60 CFM to 5-15CFM (depending on the fabric substrate and type of PTFE membrane). Under normal conditions Baghouse.com PTFE membrane filters will operate at 0.5in pressure drop at a 6:1 air-to-cloth ratio. With time additional dustcake formation will lead to pressure drop increase.
However due to non-stick characteristics of PTFE, cleaning of the filters is easily accomplished. This will allow for a consistently low pressure drop to be maintained, which in turn results in lower energy consumption, high output, and reduced compressed air for cleaning cycles.
Applications
The following is a list of just some of the possible applications where PTFE membrane Baghouse filters have provided increased system performance for our customers. Contact a Baghouse.com representative to learn if your operation could benefit from employing the latest in PTFE Baghouse filtration technology.
Cement & Stone
- Kiln Clinker
- Cooler Crushing
- Grinding Raw Mill/Finish Mill
- Packing Machines
- Kaolin Processing
- Material Loading
- Material Handling/Transport
- Coal Mill
- Clay Grinding
- Bentonite Crushing
- Silo Bin Vents
- Calciners
Food/Pharmaceutical
- Food Additive Processing
- Spray Drying
- Pharmaceutical Pill Coating
- Cereal Processing
- Animal Vitamins
- Pneumatic Conveying/Material Handling
Chemical
- Fertilizer Spray Dryers
- Calcium Hypochlorite
- Polyethylene Resins
- Coke-Briquetting Process
- Tire/Specialty Rubbers
- Catalyst Manufacturing
- Plastic Fibers
- Cellulose Fibers
- Polystyrene Fluff
- Packaging
- PVC
- Detergents
Paint/Pigments
- Toner Mixing/Blending
- Pneumatic Conveying
- Pigment Blending
- Micronizers
- Packaging
- Paint Mixing
- Spray Dryers
Combustion
- Boiler
- Coal Handling
- Fly Ash Handling
- Hazardous Waste
- Incinerators
- Soil Remediation
- Waste to Energy
- Corbon Black
- Fume Metal Oxide
Metals
- Electric Arc Furnace
- Desulphurization Furnace
- Induction Furnaces
- Mold Cooling Lines
- Shot Blast/Grinding
- Ladle Melt Furnace
- Sand Shakeout/Sand Reclaim
- BOF Furnace
- Caster
- Reverb Furnace
- Sintering