A 5-7 tons per hour (T/H) animal feed production line is a significant investment for farmers, feed manufacturers, and agribusinesses, offering an efficient solution for medium-scale operations aiming to produce high-quality animal feed. This article details the essential components required to set up a complete 5-7 T/H feed manufacturing system.
1. Raw Material Receiving and Cleaning System
The first stage in feed production involves receiving and cleaning raw materials to ensure high-quality output.
- Silos: Large storage units designed for holding bulk raw materials such as grains, seeds, and additives, tailored to the production requirements.
- Cleaning Equipment: Includes vibrating screens, magnetic separators, and pre-cleaners to remove impurities, dust, and foreign objects from raw ingredients, ensuring the purity of the feed.
2. Grinding System
The grinding process is vital for reducing raw materials to the necessary particle size for feed production.
- Hammer Mill: Typically powered by a 55 kW motor, this machine grinds raw materials like grains into fine particles, ensuring uniformity in size, which is crucial for consistent mixing and pelleting.
3. Mixing System
After grinding, the ingredients must be thoroughly mixed to achieve a homogeneous blend.
- Mixer: An 11 kW single roller double paddle mixer is used to evenly distribute all components, including essential vitamins and minerals, throughout the feed mix.
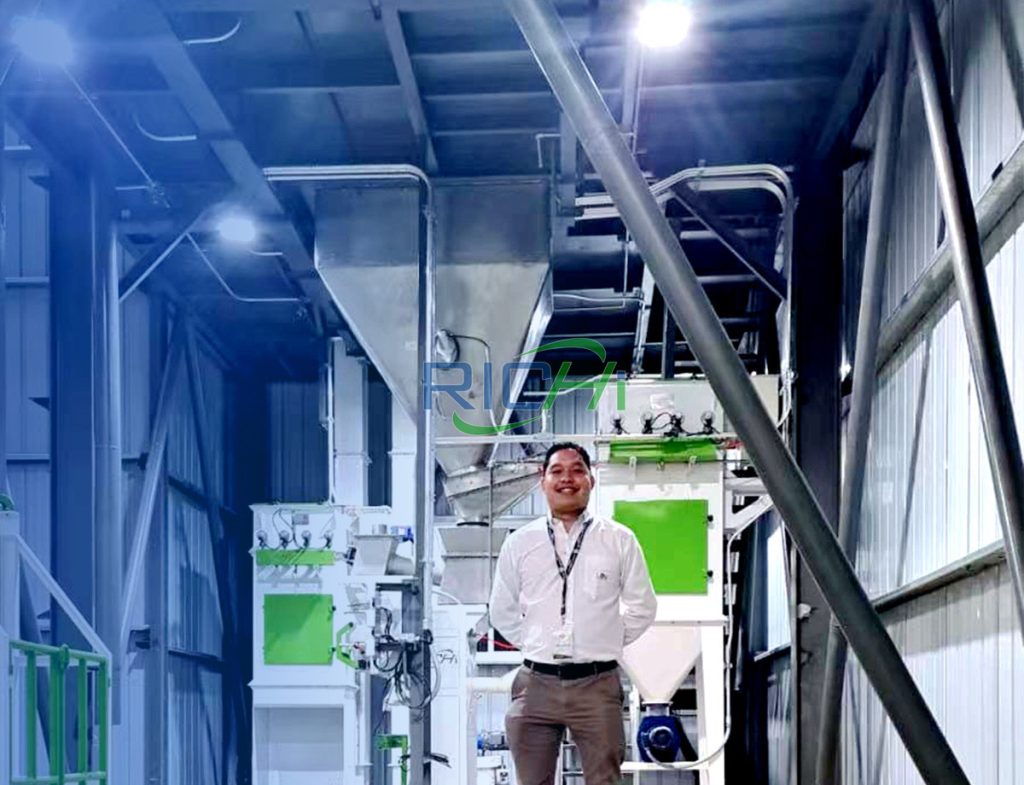
4. Batching System
Accurate batching is critical to maintain the quality and consistency of the feed.
- Batching Scales: Automated scales that precisely measure and dispense each ingredient according to specific feed formulations, ensuring uniformity in every batch.
5. Pelleting System
In this stage, the mixed feed is compressed into pellets.
- Pellet Mill: The core of the production line, a 55 kW feed pellet machine compresses the conditioned feed mix into pellets, typically 2-8 mm in diameter, depending on the die and roller configuration.
- Conditioner: Prepares the feed mixture with steam and water to enhance pellet quality, ensuring proper moisture content and pellet durability.
6. Cooling System
Post-pelleting, the hot pellets must be cooled to prevent spoilage.
- Counter-Flow Cooler: Cools the pellets to ambient temperature, preparing them for packaging and storage while preserving their quality and nutritional integrity.
7. Screening and Crumbling System
To ensure uniform pellet size, a screening and crumbling system is employed.
- Vibrating Screen: Separates pellets by size, removing fines and oversized pellets to ensure consistency in the final product.
- Pellet Crumbler: Breaks down any oversized pellets into smaller, uniform pieces, ensuring all feed pellets meet the required specifications.
8. Packing System
The final step involves packaging the finished feed for distribution.
- Packing Machine: A DSC-50 packing machine weighs and bags the feed pellets, typically in 25 kg or 50 kg bags, ensuring accuracy in weight and secure sealing.
9. Dust Collection System
Maintaining a clean and safe production environment is essential.
- Dust Collector: A box cylinder pulse dust remover captures airborne dust generated during grinding and pelleting, improving air quality and reducing fire hazards.
10. Control and Automation System
Modern feed production lines often include advanced control systems for efficiency and precision.
- PLC Control Center: A programmable logic controller (PLC) automates and monitors the entire production process, allowing operators to adjust parameters for optimal performance.
- Sensors and Monitors: Track critical parameters like temperature, moisture, and flow rates, ensuring a consistent and efficient production process.
Conclusion
A 5-7 T/H animal feed pellet production line consists of several key components, each playing a crucial role in producing high-quality feed. From raw material handling and cleaning to grinding, mixing, pelleting, cooling, screening, and packing, the equipment outlined above forms the backbone of a successful feed manufacturing operation.
Investing in a comprehensive feed production system not only boosts productivity but also ensures the final product meets the nutritional requirements of livestock. Understanding the essential equipment involved allows operators to make informed decisions when establishing their feed production facilities, ultimately contributing to the success and sustainability of their agricultural ventures. As demand for quality animal feed grows, a well-designed production line will be vital for meeting market demands and ensuring profitability.