The production of wheat straw pellets has gained significant attention as a sustainable source of biofuel and animal bedding. The efficiency of the pelletization process is heavily influenced by the performance of the wheat straw pellet machine. This article explores the key factors related to the machine’s performance and how they impact the overall production efficiency.
1. Importance of Consistent Material Flow
Maintaining a consistent flow of wheat straw into the pellet machine is crucial for efficient production. Inconsistent feeding can lead to fluctuations in pressure within the pelleting chamber, resulting in poor pellet quality and increased wear on machine components.
- Feeder Design: The design of the feeding system, such as screw feeders or belt feeders, plays a significant role in ensuring a steady and uniform supply of straw. Well-designed feeders can handle the fibrous nature of wheat straw effectively, preventing clogs and ensuring consistent material flow.
- Moisture Content: The moisture content of the wheat straw should be carefully controlled, typically between 10-15%, to optimize the feeding process. Excessively dry or wet straw can cause issues with material flow and lead to reduced production efficiency.
2. Impact of Particle Size Reduction
Proper size reduction of wheat straw is essential for achieving high-quality pellets and maintaining the efficiency of the pellet machine.
- Crusher Performance: The crusher, often a hammer mill or knife mill, is responsible for breaking down the straw into smaller particles, typically less than 5 mm in size. The efficiency of the crusher directly affects the particle size distribution and, consequently, the pelleting process.
- Wear on Machine Components: Poorly crushed straw with inconsistent particle sizes can increase wear on the pellet mill components, such as the die and rollers. This leads to more frequent maintenance and reduced machine lifespan.
3. Conditioning Process and Its Influence
The conditioning process prepares the wheat straw for pelleting by adding moisture and heat, enhancing its binding properties.
- Moisture Addition: The conditioner ensures that the straw reaches the ideal moisture content for pelleting, typically between 10-15%. Precise moisture control is essential for achieving high-quality pellets and maintaining production efficiency.
- Heat Application: Applying heat during conditioning helps soften the straw fibers, improving their binding characteristics. Effective heat distribution ensures uniform conditioning and enhances the overall efficiency of the pelleting process.
4. Die and Roller Performance
The die and rollers are the core components of the pellet mill, responsible for compressing the straw into pellets. Their performance directly impacts the quality and consistency of the final product.
- Die Design: The design of the die, such as the hole size and distribution, affects the pressure and temperature within the pelleting chamber. A well-designed die can optimize the pelleting process, leading to higher production efficiency.
- Roller Pressure: The rollers apply pressure to the straw, forcing it through the die holes. Maintaining optimal roller pressure is crucial for achieving consistent pellet density and size. Improper pressure can lead to pellet breakage and reduced production output. (Related post: straw pellet machine)
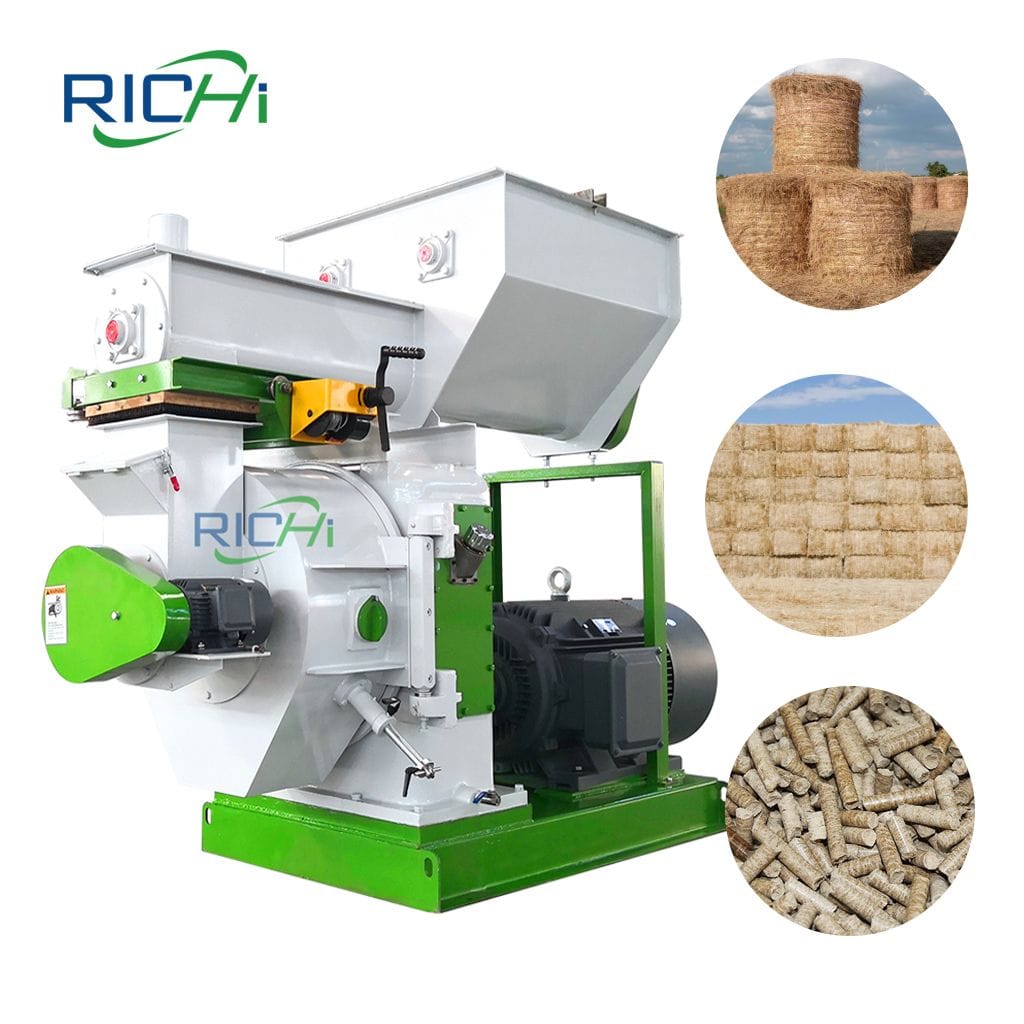
5. Cooling System Efficiency
After the pellets are formed, they must be cooled to stabilize their structure and prevent spoilage. The efficiency of the cooling system can impact the overall production process.
- Cooling Rate: An effective cooling system, such as a counterflow cooler, can quickly reduce the temperature of the pellets while minimizing moisture loss. Rapid cooling helps maintain pellet quality and prevents bottlenecks in the production process.
- Consistent Pellet Quality: Proper cooling ensures that the pellets maintain their shape and size, reducing the amount of fines and breakage. This consistency in pellet quality contributes to higher production efficiency and reduced waste.
6. Maintenance and Wear Resistance
Regular maintenance and the wear resistance of the wheat straw pellet machine components are crucial for maintaining production efficiency over time.
- Preventive Maintenance: Implementing a preventive maintenance program, including regular inspections, lubrication, and component replacements, can help minimize downtime and ensure optimal machine performance.
- Wear-Resistant Materials: Using high-quality, wear-resistant materials in the construction of the pellet machine components, such as the die and rollers, can extend their lifespan and reduce the frequency of replacements. This contributes to consistent production efficiency and lower maintenance costs.
7. Automation and Control Systems
Integrating advanced automation and control systems can enhance the efficiency and consistency of the wheat straw pellet production process.
- Monitoring and Adjustment: Real-time monitoring of key parameters, such as temperature, pressure, and feed rate, allows operators to make timely adjustments to optimize the production process. This automation reduces the likelihood of human error and enhances overall efficiency.
- Data Collection and Analysis: Automated control systems can collect and analyze production data, enabling operators to identify trends, optimize settings, and make data-driven decisions to improve efficiency over time.
Conclusion
The performance of a wheat straw pellet machine is a critical factor in determining the overall production efficiency. By focusing on consistent material flow, effective particle size reduction, optimal conditioning, die and roller performance, efficient cooling, preventive maintenance, and advanced automation, producers can maximize the efficiency of their wheat straw pellet production process.Investing in high-quality machinery and implementing best practices in machine operation and maintenance will contribute to the success and sustainability of wheat straw pellet production. As the demand for renewable energy sources and eco-friendly animal bedding continues to grow, optimizing the performance of wheat straw pellet machines will be essential for maintaining a competitive edge in the market.