The rice straw pellet making machine is a specialized piece of equipment designed to convert rice straw, an abundant agricultural byproduct, into high-density pellets. These pellets can be used as a renewable energy source, animal bedding, or as a component in various industrial applications. Understanding the main components of a rice straw pellet making machine is essential for optimizing its performance, ensuring product quality, and maintaining operational efficiency. This article explores the key components of a rice straw pellet making machine and their respective functions.
1. Feeding System
The feeding system is the first component of the rice straw pellet making machine. It plays a crucial role in regulating the flow of raw materials into the machine.
- Types of Feeders: Common types of feeders include screw feeders and belt feeders. Screw feeders are often used for their ability to provide a consistent flow of material, while belt feeders are useful for handling larger volumes of straw.
- Importance of Consistency: A reliable feeding system ensures a steady and uniform supply of rice straw to the pellet mill. Inconsistent feeding can lead to fluctuations in pressure within the pelleting chamber, resulting in poor pellet quality and increased wear on machine components.
2. Crusher
Before the rice straw can be processed into pellets, it must be reduced to an appropriate size. The crusher is responsible for this initial step.
- Particle Size Reduction: The crusher breaks down the rice straw into smaller pieces, typically less than 5 mm in size. This size reduction is essential for ensuring uniformity during the pelleting process.
- Types of Crushers: Various types of crushers can be used, including hammer mills and knife mills. Hammer mills are commonly preferred for their ability to handle fibrous materials effectively.
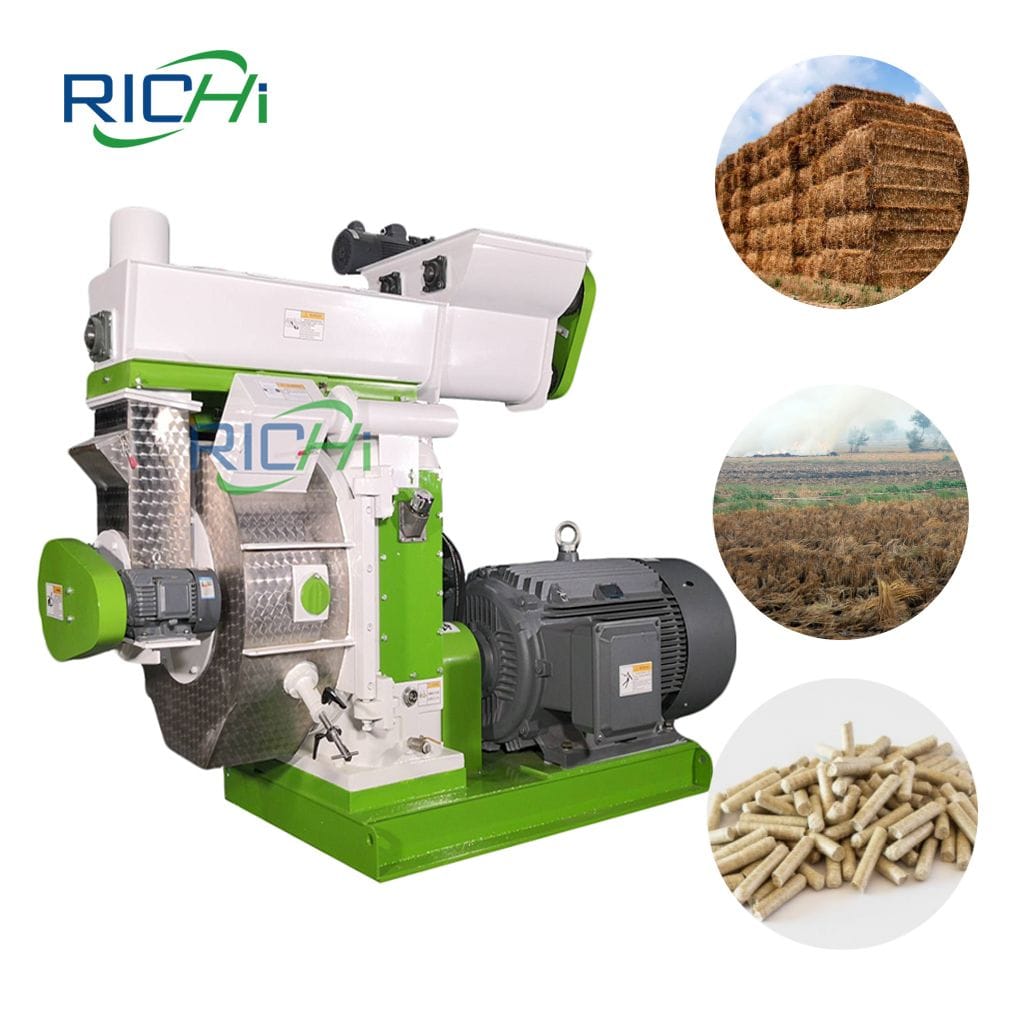
3. Conditioner
The conditioning process is critical for preparing the rice straw for pelleting. The conditioner adds moisture and heat to the raw material, enhancing its binding properties.
- Moisture Addition: The ideal moisture content for rice straw pellets is typically between 10% and 15%. The conditioner ensures that the straw reaches this moisture level, which is essential for achieving high-quality pellets.
- Heat Application: Conditioning also involves applying heat to soften the straw fibers. This process improves the binding characteristics of the material, resulting in stronger and more durable pellets.
4. Pellet Mill
The pellet mill is the heart of the rice straw pellet making machine. It compresses the conditioned rice straw into pellets.
- Components of the Pellet Mill: The pellet mill consists of a die and rollers. The die has holes through which the material is forced, while the rollers apply pressure to compress the straw into pellets.
- Die Types: The type of die used can affect the quality and size of the pellets produced. Ring die pellet mills are commonly used for their efficiency and ability to produce high-quality pellets.
- Pressure and Temperature Control: Maintaining optimal pressure and temperature within the pellet mill is crucial for achieving consistent pellet quality. Operators must monitor these parameters closely to ensure efficient operation.
5. Cooling System
Once the pellets have been formed, they need to be cooled to stabilize their structure and prevent spoilage.
- Cooling Process: The cooling system typically uses air to reduce the temperature of the pellets after they exit the pellet mill. Effective cooling helps to minimize moisture loss and ensures that the pellets maintain their shape.
- Types of Coolers: Counterflow coolers are commonly used in pellet production. They allow for efficient heat exchange, cooling the pellets while minimizing moisture loss. (Related post: corn stalk pellet machine)
6. Screening System
After cooling, the pellets are screened to remove any fines and ensure uniformity in size.
- Importance of Screening: Screening is essential for maintaining the quality of the final product. Fines can affect the combustion properties of the pellets and may lead to increased dust during handling.
- Types of Screens: Vibrating screens are often used to separate fines from the finished pellets. The design of the screen should allow for efficient separation while minimizing product loss.
7. Packaging System
The final step in the rice straw pellet production process is packaging the pellets for storage or distribution.
- Automated Packaging: Automated packaging systems can significantly enhance efficiency by reducing the time and labor required for packaging. These systems can weigh, fill, and seal bags of pellets quickly and accurately.
- Quality Control: Proper packaging is crucial for maintaining pellet quality during storage and transportation. Packaging materials should be moisture-resistant and durable to protect the pellets from environmental factors.
8. Control System
A control system is essential for monitoring and managing the various components of the rice straw pellet making machine.
- Automation: Modern pellet machines often incorporate automated control systems that allow operators to monitor key parameters, such as temperature, pressure, and feed rate, in real-time. This automation enhances operational efficiency and reduces the likelihood of human error.
- Data Logging: Advanced control systems may also include data logging capabilities, enabling operators to track production metrics over time. This information can be valuable for identifying trends and optimizing the production process.
9. Conclusion
The rice straw pellet making machine consists of several key components, each playing a vital role in the production process. Understanding the functions and importance of the feeding system, crusher, conditioner, pellet mill, cooling system, screening system, packaging system, and control system is essential for optimizing performance and ensuring high-quality pellet production.Investing in high-quality components and maintaining them properly will contribute to the overall success and sustainability of rice straw pellet production operations. As the demand for renewable energy sources continues to grow, optimizing the use of rice straw and other biomass materials will be crucial for maintaining a competitive edge in the market. By focusing on the main components of the rice straw pellet making machine, producers can enhance efficiency, reduce costs, and improve the quality of their final product.