The biomass pellet making machine is a vital piece of equipment in the renewable energy sector, converting various biomass materials into high-density pellets for energy production, animal feed, and other applications. To achieve optimal performance and efficiency, it is essential to configure the machine’s components effectively. This article discusses the key components of a biomass pellet making machine and strategies for optimizing their configuration to enhance production efficiency and pellet quality.
1. Understanding the Key Components
A biomass pellet making machine consists of several critical components, each playing a vital role in the production process:
- Feeding System: Regulates the flow of raw materials into the machine.
- Crusher: Reduces the size of biomass materials for optimal processing.
- Conditioner: Adds moisture and heat to the raw materials, improving binding properties.
- Pellet Mill: Compresses the conditioned biomass into pellets using a die and rollers.
- Cooling System: Cools the pellets after formation to stabilize their structure.
- Screening System: Removes fines and ensures uniform pellet size.
- Packaging System: Packages the finished pellets for storage or distribution.
2. Optimizing the Feeding System
The feeding system is crucial for maintaining a consistent flow of raw materials into the pellet machine.
- Type of Feeder: Choose a feeder that suits the characteristics of the biomass being processed. For example, screw feeders are effective for fibrous materials, while belt feeders may be better for bulkier materials.
- Adjustable Feed Rate: Implement a feeder with an adjustable feed rate to accommodate variations in raw material density and moisture content. This flexibility helps maintain a steady flow of material, preventing fluctuations that can affect pellet quality.
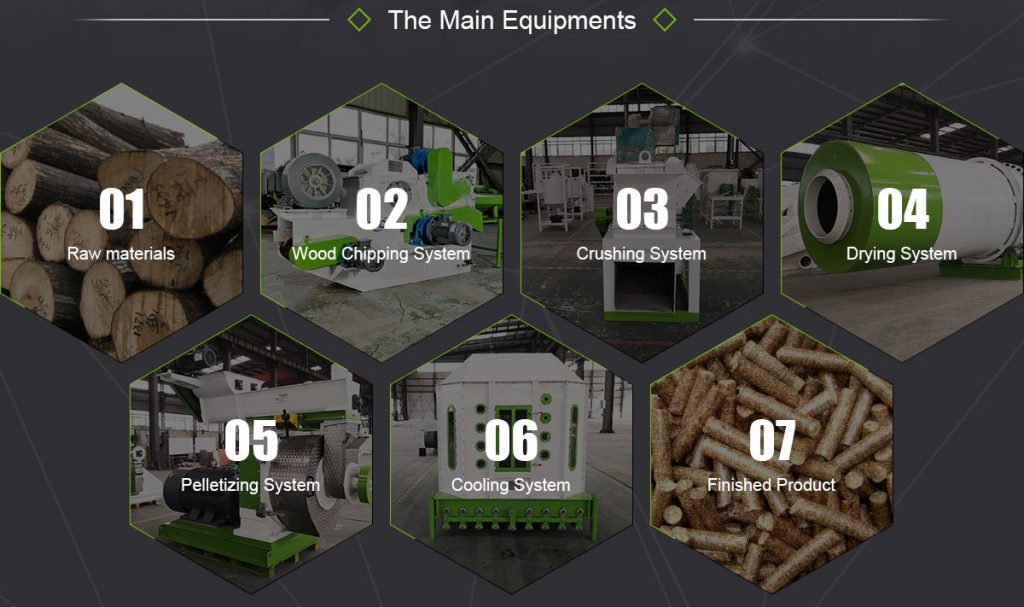
3. Enhancing the Crusher Performance
The crusher is responsible for reducing the size of biomass materials, which is essential for efficient pelleting.
- Size Reduction Efficiency: Select a crusher that can effectively reduce biomass to the desired particle size, typically less than 5 mm. A hammer mill with adjustable screen sizes can provide versatility in particle size reduction.
- Maintenance and Durability: Choose a crusher made from high-quality materials that can withstand the abrasive nature of biomass. Regular maintenance, including blade sharpening and component inspections, is essential for ensuring consistent performance.
4. Improving the Conditioning Process
Conditioning is a critical step that prepares the biomass for pelleting by adding moisture and heat.
- Moisture Control: Implement a conditioning system that allows for precise control of moisture levels. The ideal moisture content for biomass pellets is typically between 10% and 15%.
- Steam Conditioning: Use steam during the conditioning process to improve the binding properties of the biomass. A well-designed conditioner can enhance heat distribution, ensuring uniform conditioning throughout the material.
5. Optimizing the Pellet Mill
The pellet mill is the core component responsible for compressing the biomass into pellets.
- Die and Roller Quality: Invest in high-quality dies and rollers made from wear-resistant materials. The design of the die, including hole size and distribution, affects the pressure and temperature within the pelleting chamber, influencing pellet quality.
- Pressure and Temperature Control: Maintain optimal pressure and temperature settings during the pelleting process. Monitoring these parameters and making necessary adjustments can lead to improved pellet density and durability.
6. Enhancing the Cooling System
Cooling is essential for stabilizing the pellets after they are formed.
- Cooling Efficiency: Use a counterflow cooler that allows for efficient heat exchange, cooling the pellets while minimizing moisture loss. Rapid cooling helps maintain the structural integrity of the pellets and ensures they are ready for packaging.
- Airflow Distribution: Ensure that the cooling system provides even airflow distribution across the pellets. Uneven cooling can lead to inconsistencies in pellet quality and moisture content.
7. Optimizing the Screening System
The screening system is responsible for removing fines and ensuring uniform pellet size.
- Screen Design: Use vibrating screens that allow for efficient separation of fines from the finished pellets. The design of the screen should minimize product loss while ensuring that only pellets of the desired size proceed to packaging.
- Regular Maintenance: Regularly inspect and clean the screening system to prevent blockages and ensure optimal performance. A well-maintained screening system contributes to consistent pellet quality.
8. Improving the Packaging System
The packaging system is the final step in the pellet production process, and its efficiency can impact overall productivity.
- Automated Packaging: Invest in automated packaging systems that can quickly and accurately fill, weigh, and seal bags of pellets. Automation reduces labor costs and increases throughput.
- Quality Control in Packaging: Ensure that the packaging materials are moisture-resistant and durable to protect the pellets during storage and transportation. Proper packaging helps maintain pellet quality and reduces spoilage.
9. Implementing Control Systems
Advanced control systems can enhance the overall efficiency of the biomass pellet making machine.
- Real-Time Monitoring: Implement real-time monitoring systems that track key parameters such as temperature, pressure, and feed rate. This data allows operators to make timely adjustments to optimize the production process.
- Data Analysis: Utilize data analysis tools to identify trends and areas for improvement in the production process. Analyzing historical data can help optimize component configurations and enhance overall efficiency.
Conclusion
Optimizing the component configuration of a biomass pellet making machine is essential for enhancing production efficiency and ensuring high-quality pellets. By focusing on the feeding system, crusher, conditioner, pellet mill, cooling system, screening system, packaging system, and control systems, producers can improve the performance of their machines and achieve better operational outcomes.Investing in high-quality components and implementing best practices for maintenance and monitoring will contribute to the long-term success and sustainability of biomass pellet production operations. As the demand for renewable energy sources continues to grow, optimizing the use of biomass materials through effective machine configuration will be crucial for maintaining a competitive edge in the market. By prioritizing these optimization strategies, producers can enhance efficiency, reduce costs, and improve the quality of their final product. (Related post: Biomass Pellet Machine For Sale)