Rotary airlock feeder, also known as a rotary airlock valve or rotary feeder, is a critical component in pneumatic conveying systems and bulk material handling processes. This device plays a dual role: it serves as an airlock, preventing air from entering or exiting the system, and as a feeder, regulating the flow of bulk solid materials. Here’s a closer look at its functionality, design features, and applications:
Functionality and Performance Data
- Conveying Capacity: Rotary airlock feeders can handle a wide range of material flow rates, typically from a few cubic feet per hour (CFH) to over 10,000 CFH, depending on the size of the feeder and the material characteristics.
- Pressure Differential Handling: They are designed to withstand differential pressures up to 20 psi, making them suitable for high-pressure pneumatic conveying systems.
- Efficiency: By minimizing air leakage, rotary airlock feeders can achieve efficiency rates upwards of 99% in terms of sealing capabilities, significantly reducing energy consumption in pneumatic systems.
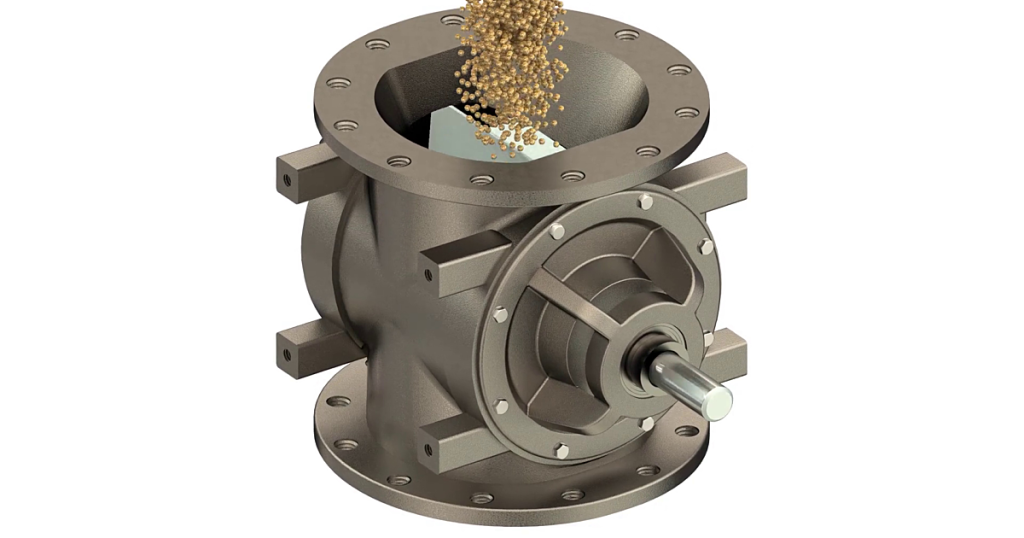
Design Features
- Rotor Speed: The rotational speed of the rotor can vary from 10 to 30 rotations per minute (RPM), with the speed affecting both the material feed rate and the effectiveness of the airlock.
- Size and Capacity: The sizes of rotary airlock valves range from 4 inches to 36 inches in diameter, allowing them to be used in a wide range of applications from small batch processing to large-scale industrial systems.
- Material Construction: The choice of material for construction can significantly impact the valve’s longevity and performance. For example, cast iron is common for general applications, while 316 stainless steel is preferred for food-grade applications due to its resistance to corrosion and ease of cleaning.
Applications
- Pneumatic Conveying Efficiency: In systems designed for the food industry, maintaining an air pressure differential of 15 psi can increase the conveying distance by up to 50%, highlighting the importance of an effective airlock.
- Dust Collection Efficiency: In dust collection systems, the use of rotary airlock feeders can improve filtration efficiency by ensuring continuous removal of collected material without disrupting the pressure differential across the filter media.
- Energy Savings: By optimizing the air seal and regulating material flow, rotary airlock feeders can reduce air leakage in pneumatic conveying systems, leading to energy savings of up to 30% in some applications.
Conclusion
Rotary airlock feeders, with their specific design parameters and operational capacities, are vital components in numerous industrial processes. Their ability to efficiently handle a broad range of material flow rates, withstand significant pressure differentials, and reduce energy consumption through effective sealing makes them indispensable in ensuring the smooth and efficient operation of bulk material handling and pneumatic conveying systems across various sectors.